Floating dryers are employed for the uninterrupted drying of painted electrical steel strips, utilizing a continuous throughput principle.
Operating on the floating principle, both the dryer and the cooling section support the moving strip during the processes of heating, drying, and air cooling on an air cushion. The well-established OTTO JUNKER floating nozzle system ensures a high level of heat input and maintains a stable, contact-free, and product-friendly transport of the strip. The combination of elevated heat input and precise centering capabilities facilitates high throughput rates with a minimized plant length.
Benefits at a glance:
- High temperature uniformity
- High throughputs with minimal plant length
- OTTO JUNKER floating nozzle system
- Efficient waste heat utilization
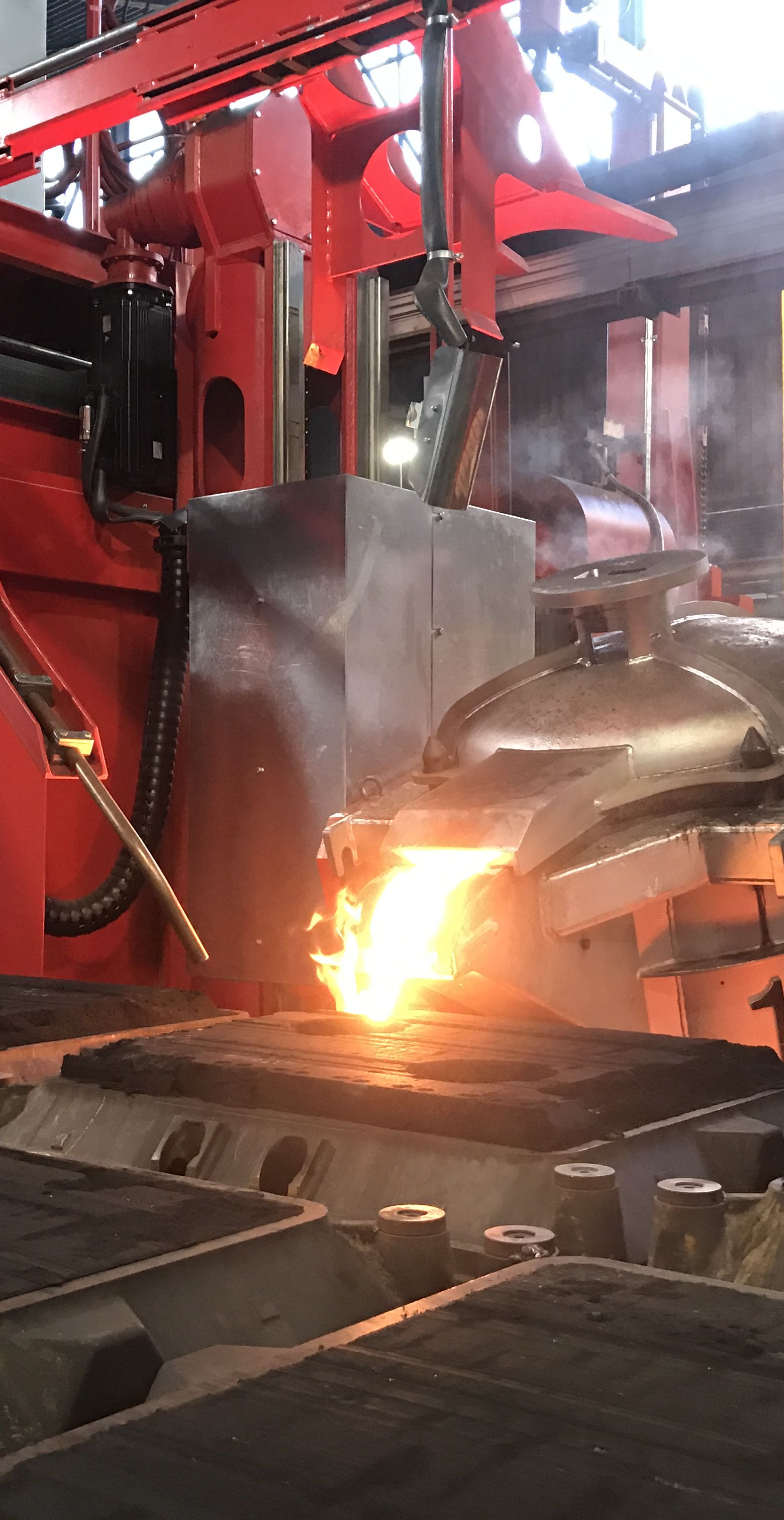
Floating dryers are employed for the continuous drying of painted electrical steel strips using a continuous throughput principle.
The dryer and the cooling section operate on the floating principle, supporting the moving strip during heating, drying, and air cooling on an air cushion. The proven OTTO JUNKER floating nozzle system ensures high heat input and a stable, contact-free, and product-friendly transport of the strip. The high heat input and perfect centering properties allow for high throughputs with minimal plant length.
Given the optimal placement of ventilators and the heating system, the system is ideally suited for installation beneath the platform of the annealing furnace. The dryer is installed in the direction of the strip behind the coating chamber. The moving strip is heated to the desired temperature, allowing the paint to dry and cure.
After passing through the dryer, the strip is cooled to the exit temperature in the cooling section.
Both the dryer and the cooling section are designed as floating belt systems. The recirculation rates are dimensioned to support the passing strip with an air cushion during heating, drying, and cooling. As a result, the strip does not come into contact with mechanical parts during heating, holding, and cooling, keeping the strip surfaces free from damage. Additionally, the recirculation systems have a centering effect on the strip. If the strip deviates laterally from the center of the nozzle array, an aerodynamic centering counterforce acts on the strip, pushing it back towards the center of the system.
Each zone is equipped with two separate recirculation fans to separately affect the top and bottom of the strip. This optimizes both the heating rate and the height of the strip in the floating furnace or cooling section.
The dryer is equipped with a process air system for the safe removal of solvents. This system keeps the solvent content in the furnace atmosphere below the lower explosive limit (LEL) in accordance with applicable explosion protection standards.
Bandwidth | 1,000 - 2,000 mm |
strip thickness | 0.1 - 0.8 mm |
belt speed | max. 180 m/min |
Downloads
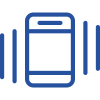
Phone +49 2473 601-0
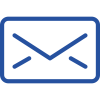
E-Mail sales@otto-junker.com